Segmented Pressure Regulation System for Hot Plate Steam Inlet
The hot plate pipeline adopts a straight in /out design according to our company's design, ensuring that the outlet from the pressure control valve to the drainage end is in a zero pressure difference state without resistance. The temperature and pressure reach the normal theoretical corresponding value (with an allowable instrument system error of ± 2-3 ℃), which can meet the process requirements of normal production. From the perspectives of economy, production rationality, and product quality control, our experience believes that the hot plate is divided into three stages for pressure regulation and steam supply. Not only can it provide the most appropriate heat by setting during the production of 3 or 5 layers of boards, good or bad materials, but it can also reduce heat loss during the production process. It can also adjust the production of different types of cardboard to the most suitable temperature, improve the quality of cardboard, and make thermal economy the most reasonable. Under the setting pressure, the stability of temperature will not be affected by the speed of production.
The Preheating Cylinder Adopts Steam Secondary Utilization
The preheating cylinder has a larger range of wrap adjustment, and the process requires that the temperature of the cardboard entering the hot plate should not exceed 100 ℃. We believe that using secondary flash steam as the main steam supply method is reasonable and scientific. And it can ensure that the pressure of each preheating cylinder is artificially adjustable between 0.3-0.8MPA (equivalent to temperature adjustable between 130-160 ℃). In order to improve the pressure difference balance pipe and piping method of the condensate water outlet pipeline, a new drainage system has been designed. Each preheating cylinder is equipped with an independent drainage valve, which can ensure that the temperature difference of each preheating cylinder is controlled at around 5 ℃. Ensure that it can meet any production speed, and reduce the drainage temperature.
Single Facer Steam
The drainage system of the corrugator has been redesigned, and each preheating certificate in the corrugator uses its own drainage system independently. The pressure difference balance is reasonably set to ensure smooth drainage. The corrugating roll and pressure roll are equipped with temperature monitoring points to ensure smooth drainage and sufficient temperature. The condensate water is discharged to achieve true secondary utilization. When the pressure is insufficient, heat is replenished through a steam booster jet pump to ensure sufficient amount of steam supplied to the two preheating cylinders, achieving high production efficiency and energy conservation.
Intelligent PLC Refines the Entire Control System
This system provides an open operation platform, and users can set the most reasonable parameters based on experience. Siemens PLC can provide the most reliable operational guarantee. Production priority, efficient operation, and system reliability are our three major goals in design.
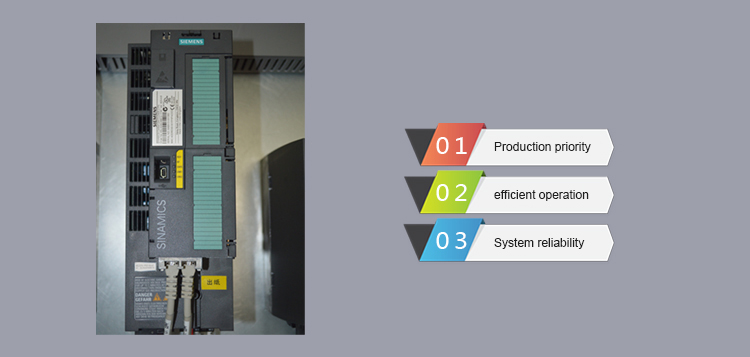
Temperature Control System Operation Advantages
(1)Shorten heating time of equipment
The heating time of traditional equipment is about 40-60min, while the heating time of the hot plate and quadruple preheating cylinder after installing the system is about 20-30 minutes, which is greatly reduced.
(2)The operating pressure of the hot plate and quadruple preheating cylinder can be controlled according to the manual setting of the production order
Changing the pressure of traditional hot plates can only be controlled by temperature locally, resulting in slow response; the drawback of four fold preheating is that the pressure cannot be controlled. The production pressure can be adjusted according to the actual production situation to meet the requirements of the production process, thereby providing assurance for cardboard production.
(3)Significantly increase the reliability of control in the production process
Due to comprehensive pressure and temperature monitoring, including corrugating roll, pressure roll, preheating cylinders, and hot plates. Even if the temperature of the hot plate is not enough, the system will automatically operate emergency response, eliminate low-temperature condensation water function, and quickly restore normal temperature, greatly reducing the occurrence of cardboard debonding caused by water blockage or poor drainage.
(4)During the production of three-layer cardboard, steam consumption can be saved
There are three, five, and seven independent operating systems in the control panel. During the production of three-layer cardboard, the non production preheating cylinder will be in standby or off state, greatly saving steam consumption.
(5)The use of secondary steam in the preheating cylinder has multiple effects
Firstly, the temperature of the discharged condensate water was reduced, improving steam utilization by 4-7%. Secondly, due to the use of leak free drainage design, there is a longer time without steam leakage compared to conventional drainage systems, greatly reducing the waste caused by back pressure and steam leakage.
(6)The purpose and function of machine pressure control
During the production of low weight cardboard, excessive heat can cause problems such as cardboard breakage and a decrease in physical indicators. To ensure the most appropriate heat supply for each machine, it is necessary to install a pressure control valve. For example, after installing a pressure control valve in the main steam supply pipe of each hot plate, the operator can perform the most suitable operation according to the order (pressure adjustment range is 0.0-1.2MPA). It not only ensures the high-speed operation of the production line, but also achieves effective control of cardboard quality. At the same time, it also saves steam compared to the original method.
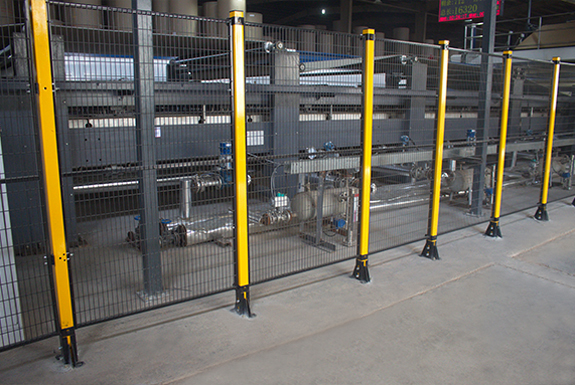
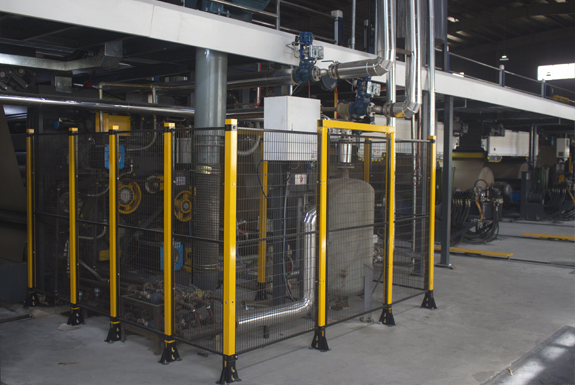